The work of Procurement Engineering does not start with the kick-off of a R&D project. There are tons of tasks prior to the design work. The following post will provide a crisp list of necessary activities and tasks before the real design work starts. Before we go into the details we need to say goodbye to the idea that procurement buys stuff engineering has designed and the we start to work once the design is finished. When procurement is invited to discuss how to set up a cross-functional team to support the newest development project the responsible procurement engineer has already a full list with different home work activities. So, what is to do …?
You need to have an overview of all running and upcoming R&D activities.
If you are not aware what is coming and what is going on right now there is no chance to support engineering at all in finding the optimal design for sourcing and manufacturing. In most companies the process is set up in a way the engineering or the R&D project manager should actively reach out to the procurement organization and tie them in. The better approach is that the procurement representative is actively participating the R&D planning. Only then there is pro-active resource planning and management possible and the risk that a project is conducted w/o procurement support is minimized.
Plan needed resources
Already in the very early planning phase of a development project the scope and the design target are known or should be known. Based on that it is possible and necessary to define the needed resources to support the project (quantity and know-how). The needed support needs to be cross-checked with the need of other projects, which may be not R&D related.
Set up a strategic supplier map
The set up of a strategic supplier map prior to the start of the project itself might be very surprising for you but is in fact one of the most important things to do. Prior the kick-off of the project itself the procurement organization should be very aware how the future supply chain should look like. Such a supplier chain “map” should be the answer to the question: “How would the most competitive supply chain for our current product portfolio look like?” Some basic rules should be the basic to develop this supplier map. E.g. there should be always dual-sourcing possible. Therefore, the task is to define two potential suppliers which should be both capable to produce the component. One supplier should be established and already known. The supplier is already producing parts and has the related manufacturing know-how. The 2nd supplier in that dual-sourcing set up should be the supplier with biggest cost-out potential / should be the most competitive supplier known on the market for this kind of component/s.
What to do w/ that list? The list should be reviewed and communicated to engineering. The message has to be: “Ensure that we can source in the future these components or the developed derivatives with these suppliers. We will support you wherever we can that you have access to the suppliers and you can co-develop the parts with them. If a new design feature designs one of these suppliers out – it has to be justified.”
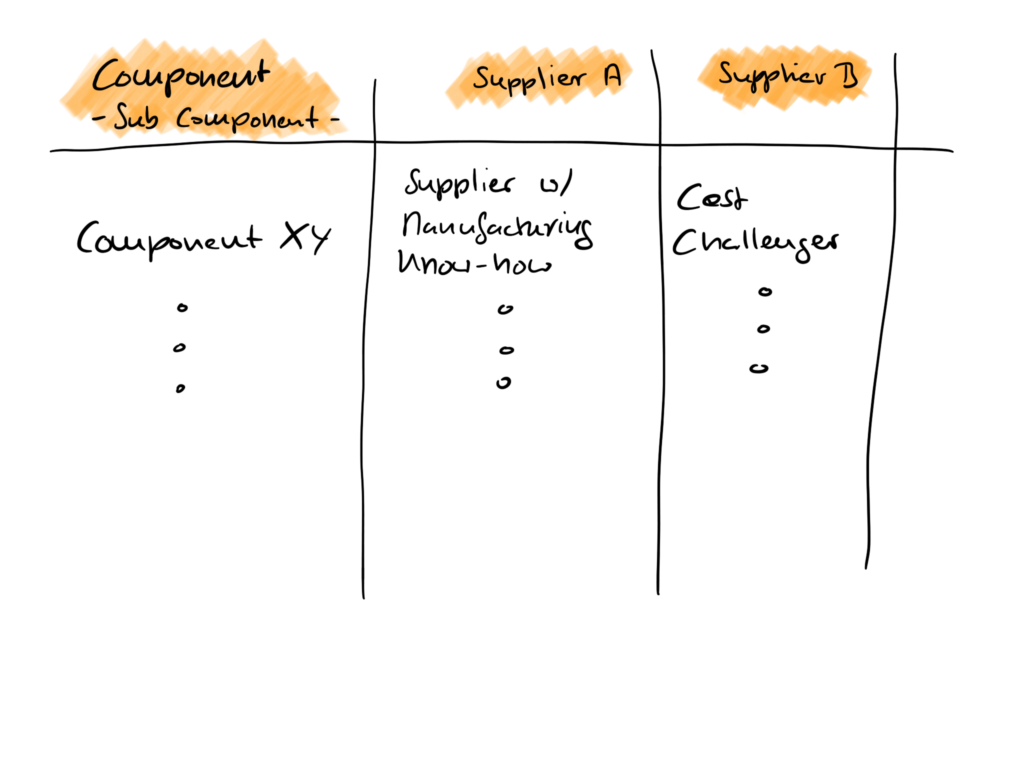
This approach somehow turns around the traditional supply chain planning. The big advantage of this set up is that it provides engineering a kind of boundary condition for the design and ensures that in the very end of the design process all components can be sourced. It must be clear that the supplier set up is not engraved in stone, but every change to it, driven by engineering, must be justified by a higher performance etc. which overcompensates the disadvantages in the supply chain set up.
Key Take Away: Pro-Activity is King. Procurement needs to develop a clear understanding how the future supply chain for a certain product should look like. This understanding should be one boundary condition for the future design concept!
I agree, a strategic supplier map is important and purchasing needs to be involved in an early stage, but not to just find the most competitve supply chain and/or to set the boundary conditions for design.
Prior to the supplier map engineering and purchasing need to jointly challenge the methods of manufacturing for the new component, because the method of manufacturing is one of the cost drivers.
If you do not take into account to challenge different potential methods of manufacturing (MoM) beforehand you possibly stick to a predefined supply chain (SC) with a not so competitive MoM. Means, the SC might be competitve for their MoM, but a different MoM could be even more competitve.
I am looking forward to read your next post soon.