If someone is asked when certain organizations shall be involved in a new project, normally the standard answer is “as early as possible”? But why? Parts are procured once they are designed and not earlier. So why should there be an additional interface in the R&D organization, which makes the whole development process more complex, time consuming, and in certain cases more difficult for the designer ;-)?
To answer this question we have to look in a first step at the targets. It is not surprising that in most cases the most important target is to meet a certain cost target while fulfilling the functional requirements (the requirements management as one tool in the procurement engineering process will be discussed in a separate post). The cost targets are in many cases regarded as utopistic, challenging, or even unfair. The engineer is alone and in many cases nobody is supporting w/ methods, processes, and know-how to meet the cost targets.
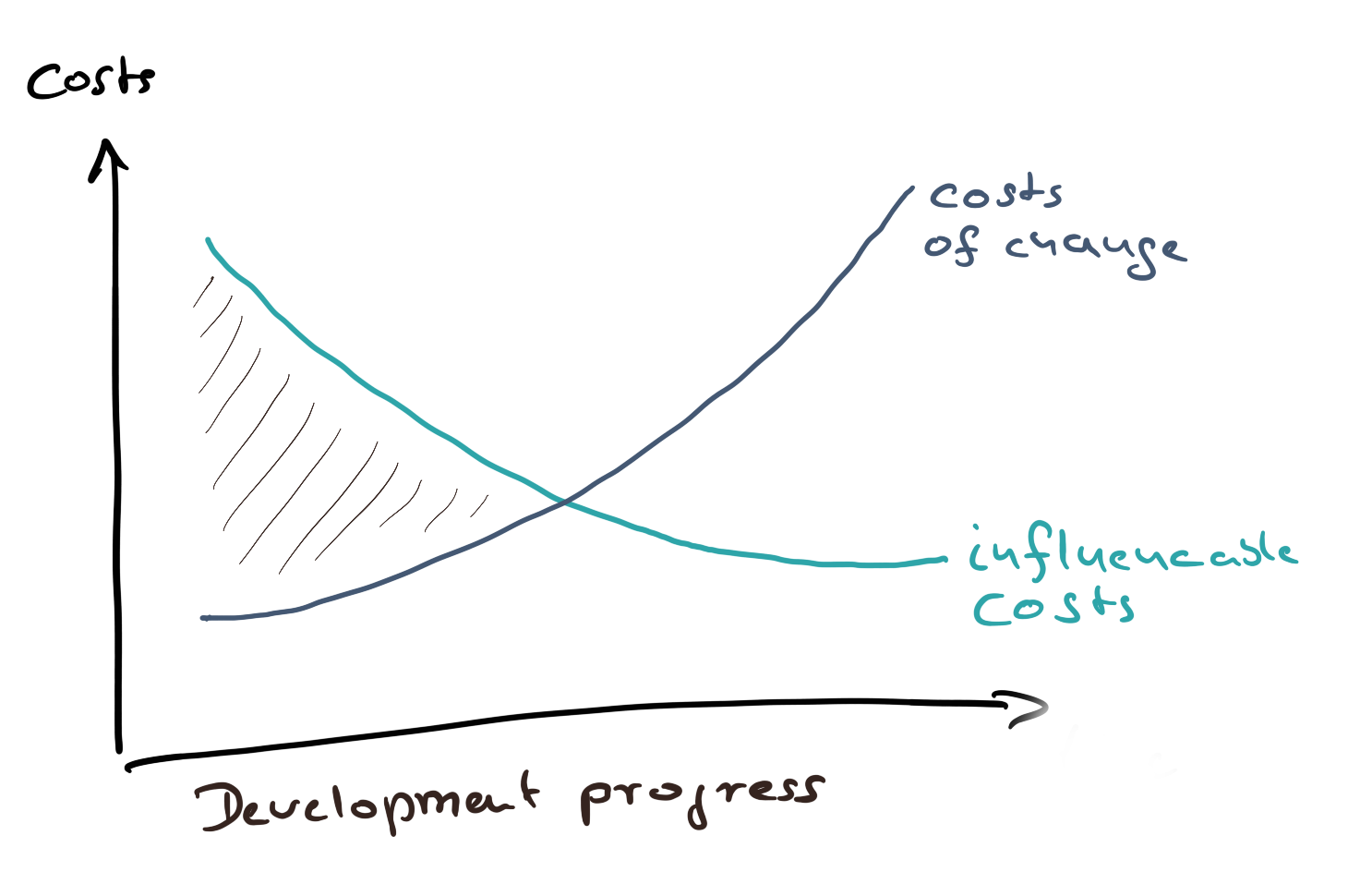
Involving the procurement is w/o doubt one key lever to support with its expertise the target cost achievement. In case of procurement involvement the statement as early as possible is indeed right. So why? To understand this you have to imagine that an R&D project consists of many different single components, which are individually developed. The interfaces between these components are managed by different layers of R&D project managers, Lead Engineers or other functions in ensure that everything works together at the end. Early in the process the interfaces are not yet defined and stable. Therefore it is possible to compare and review different concepts w/ each other and necessary adoptions to meet the interface requirements w/ other components can be easily included. So more mature the design is, so more mature are also the other interfaces. More mature means also inflexible. Great cost saving ideas late in the process may lead to necessary changes in other components. This results in definitely in costs for design changes (man hours) and in many cases also to cost increases at other components. With increasing maturity of the design so more likely it is, that the benefits are overcompensated by the necessary design efforts to adjust the interfaces. An example could be that a component was designed with a known customized material. Late in the design, a design team member (maybe form procurement), suggests a slightly different material, but for much lower costs as it is a standard material, available at “every corner”. Calculations show the the suggested material provides the necessary properties, but the different thermal material expansion behavior would require a complete new layout of the whole module and this is not justified by the savings on the direct material. If such an idea would have been brought up or considered early in the concept phase the savings could have been realized w/o problem.
Key take away: Procurement and the Engineering organization should work together as early as possible as the delta between “costs of change” and the “influencable costs” is at the beginning at a maximum and the return on invest (dedicated procurement work) is ensured.