What is the difference between Procurement and Cost Engineers and is it worth to have both in the team setup? This will be very roughly discussed by using an example and providing a guideline when this might make sense for a company. As always there is no simple answer. Some facts might help to make the decision: size of company; size of commodity, complexity of commodity & skill set of procurement engineers. Fact is that both roles (should) have at least 50% overlap in their expertise.
Currently you can find many information about Cost Engineering in the internet. Also, an amazing amount of job offers are available. It feels like a little boom for this type of engineers. Therefore, I asked myself the question – is there a “versus” or is it maybe the same role just in a new dress?
Focusing on the key elements of both jobs the requirements are very similar. The major difference is kind of a work split due to the amount of work, which in general both should be able to support from skill set point of view. Since it does not make sense just to compare all the key words from job requisitions, I would like to focus on one example.
Consider a new design of cars needs a special electrical battery housing because conventional engines are no-brainers in these days. After review of the design together with R&D the Procurement Engineer is confident to produce this part as an aluminum casting. Now the Cost Engineer work starts. Again, a review of drawings as well as best fitted manufacturing processes will be done – similar to procurement engineers work. Considering all investigations will result in aluminum casting as well, the calculation of the part performed by a technology & cost expert will provide a detailed cost break down. As an example you can see a basic break down. [see Figure 1]

In order to keep the message short and not go too much in detail we can use a simple pareto analyses for the cost break down. Just start with the highest value will lead you to focus on material cost. Majority of these material cost is Aluminum with about 40-45% of the total cost for this type of casting. (gap to 49% are other consumable materials) Knowing the costs for all other process steps and dedicated materials related to that will give you many ideas to optimize during early design phase e.g. reduce aluminum by decrease wall thickness by increase core size if outer shape cannot be changed. Even changing from casting to a purely machined part can be checked but raw material will be almost the same since this is treated on international markets (London/Shanghai).
Knowing these basics coming from cost break down, manufacturing & design changes as well as supplier decision can be made which is exactly what a procurement engineer does. For sure the processes of design & manufacturing iteration are an ongoing process with a lot of overlapping tasks. At least this will form the Cost Engineer and Procurement Engineer to be a perfect team. For big global player companies, I would suggest to decide pending on two major factors of having Cost and Procurement Engineers with two separate people on board or stay just with one person which covers both roles: 1. Purchasing volume of selected commodity 2. Complexity of the technology/commodity. [see Figure 2]
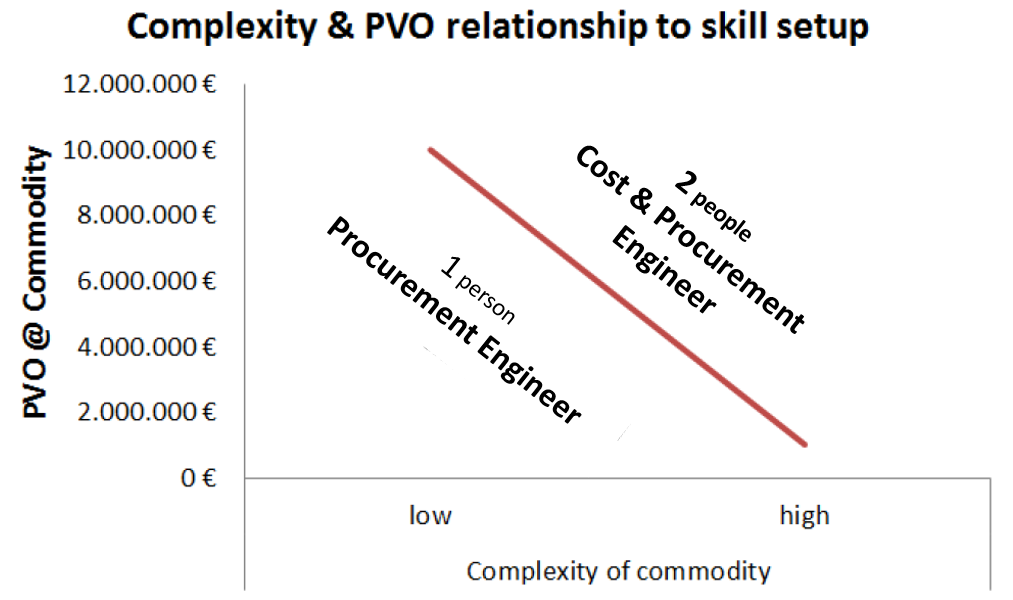
At the end I think there is a good reason for both roles as long as they have similar skill set but slightly deeper expertise in either procurement tools or cost modeling tools. Currently within companies there is still an increase of cost engineering experts which I think will be suitable for big size companies. The smaller the companies are the more they combine both roles in one person, most likely called Procurement Engineer.